Tank Lining Services
Industrial-Grade Linings for Critical Containment.
Tank Lining Repair Toronto
At B.E.S.T. Painting, we specialize in providing high-quality industrial paint solutions for various applications. We are proud to introduce our latest service: Tank Lining. This service is designed to protect and extend the life of your storage silos and bulk fuel storage tanks with advanced interior lining systems.
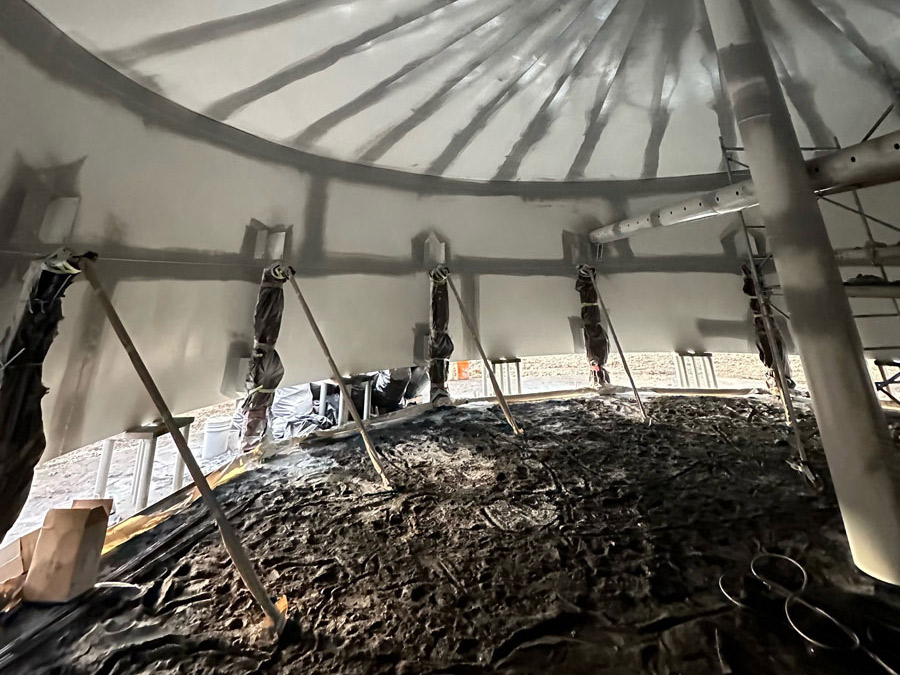
Why Choose Our Tank
Lining Services?
Our Tank Lining solutions offer superior corrosion resistance, enhanced durability, and tailored coatings based on your storage needs.
Every project is built to meet industry safety standards and is overseen by a certified NACE Level 3 Inspector—ensuring precision and long-term protection in even the harshest environments.
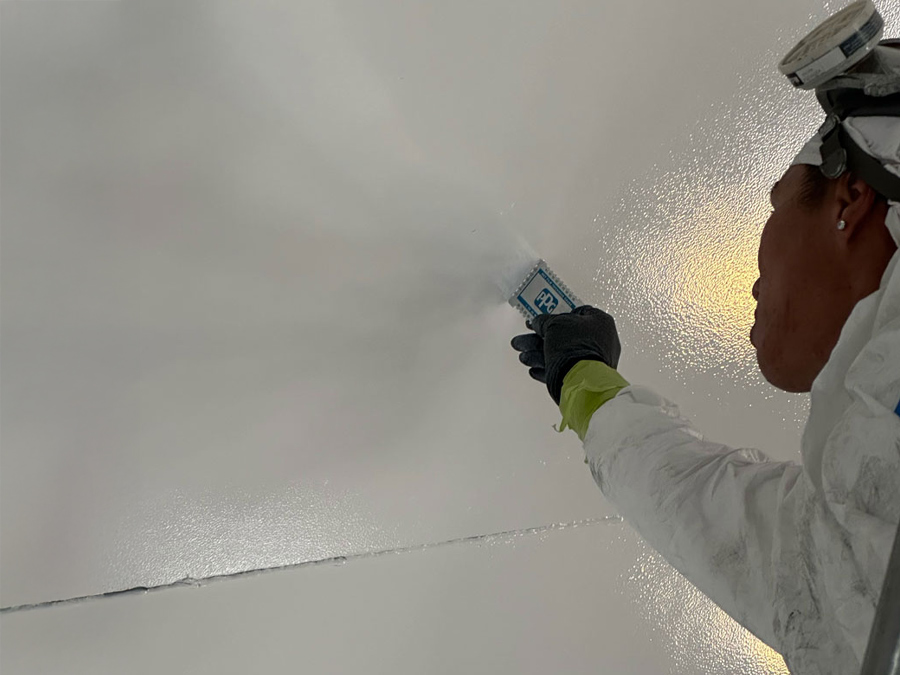
Our Process
Cleanliness & Hygiene: In industries like food processing and pharma, painted ceilings are easier to clean and help meet strict hygiene standards.
Fire Resistance: Fire-resistant coatings can slow flame spread, adding an extra layer of protection for employees and assets.
Regulatory Compliance: Aging, brittle paint can crack or peel—posing health and safety risks, potential shutdowns, or negative customer impressions.
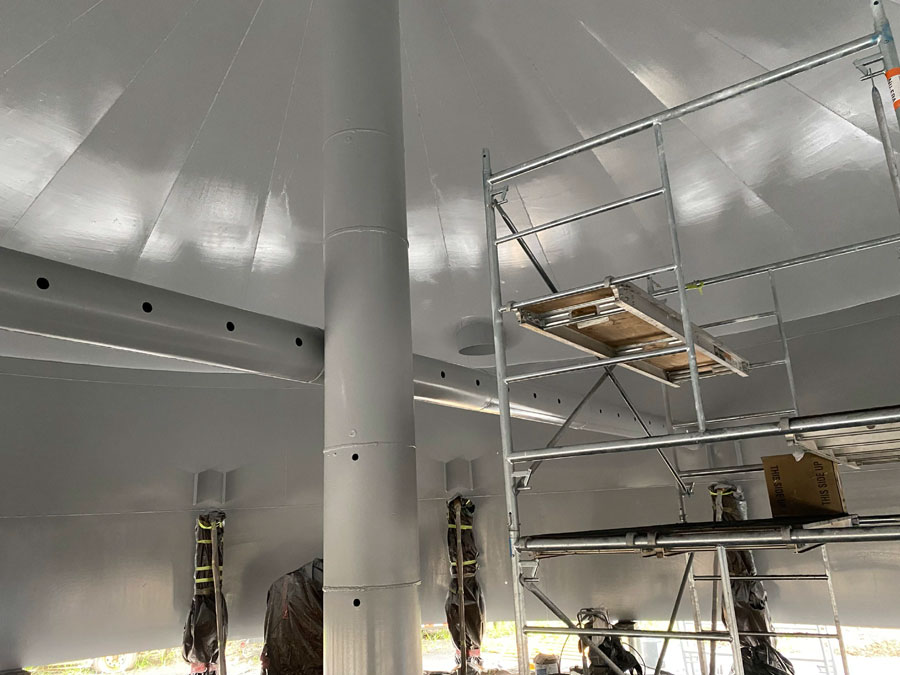
Ideal Applications for Our
Tank Lining Services
Perfect for storage silos, bulk fuel tanks, and other high-demand environments, our linings prevent corrosion, leaks, and contamination.
We follow strict safety protocols to protect both workers and your facility during every project.
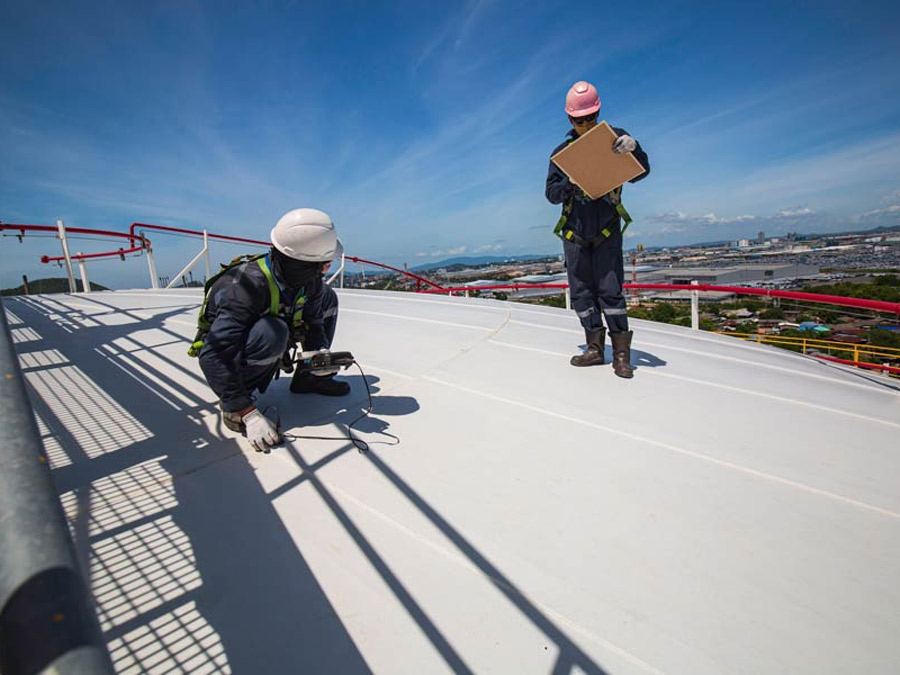
When to Inspect Your Tank Lining
Cracks, blisters, or stains: Signs of lining failure and corrosion.
Hidden corrosion: Possible under insulation, even if the lining looks fine.
Ultrasonic testing: Finds thinning or worn areas.
Spark testing: Detects pinholes and breaches.
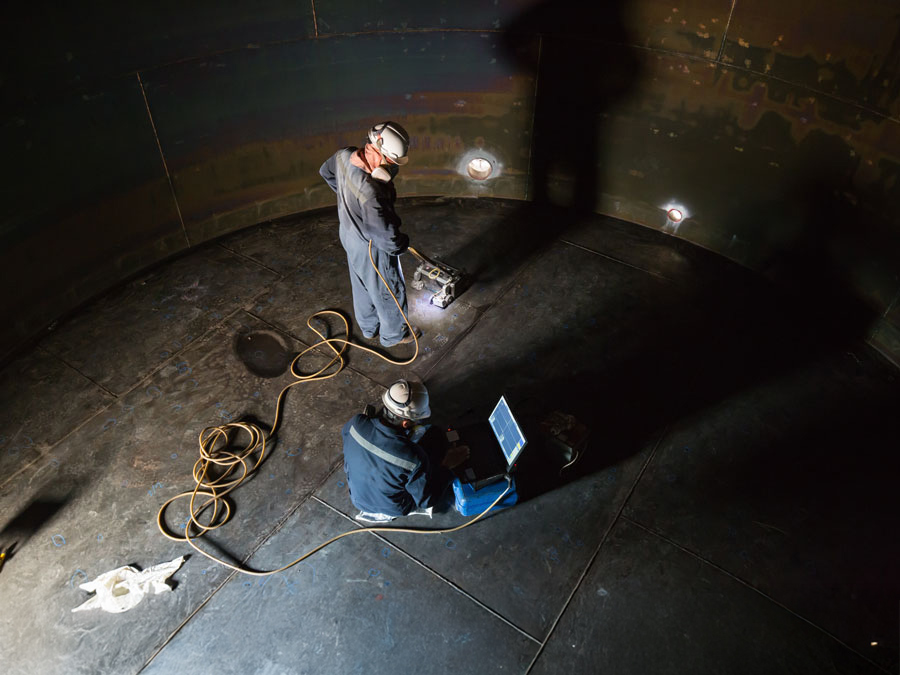
Inspection or Repair
Chemical Compatibility: If the lining degrades from chemical exposure, it may need repair or replacement.
Leaks & Seepage: Moisture at seams or joints is a red flag for lining failure.
Increased Maintenance Needs: More frequent cleaning often indicates lining breakdown.
NACE Level 3 Inspection: Certified inspections provide expert evaluations and ensure early issue detection using all key testing methods.