Preventative Maintenance
Industrial Painting Preventative Maintenance Program
In painting terms, Preventative Maintenance refers to a set of proactive measures and routine tasks that are performed to prevent or minimize the deterioration, damage, or wear and tear of coated surfaces and the underlying structures. The goal of Preventative Maintenance is to extend the life and quality of a coating job, whether it’s on walls, ceilings, exterior surfaces, or any other painted elements.
Here are some common preventative maintenance practices in the industrial painting industry:
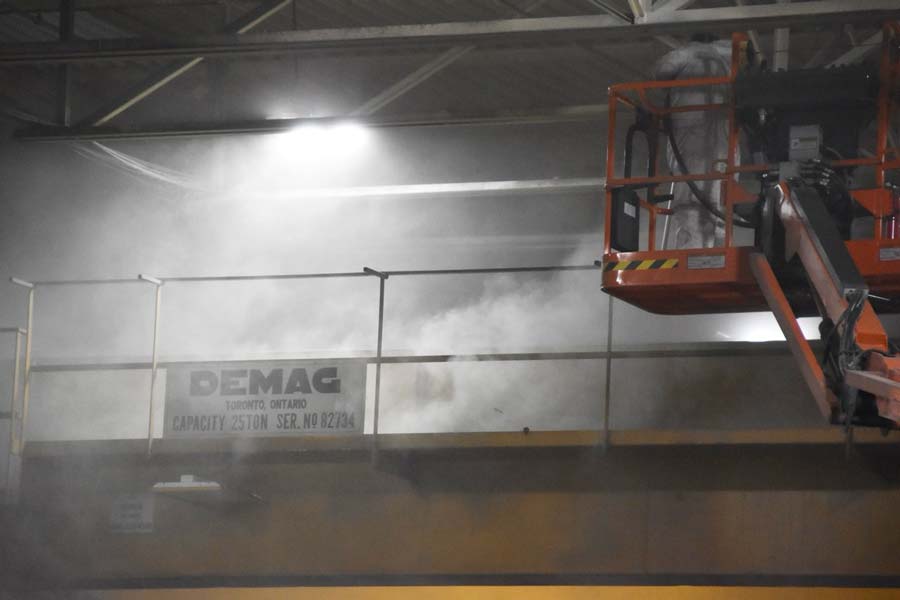
1. Cleaning: Regularly cleaning coated surfaces to remove dirt, dust, grime, and other contaminants helps prevent the accumulation of substances that can degrade the coating’s integrity.
2. Inspections: Periodic inspections allow you to identify early signs of damage, peeling, or wear. This helps you address issues before they become major problems.
3. Repairs: Promptly repairing any cracks, chips, or other imperfections in the coating can prevent further deterioration and water intrusion, especially in exterior surfaces.
4. Sealing and Caulking: Applying or reapplying sealants and caulk to gaps, joints, and seams in coated surfaces helps prevent moisture infiltration, which can lead to peeling, blistering, corrosion and rot.
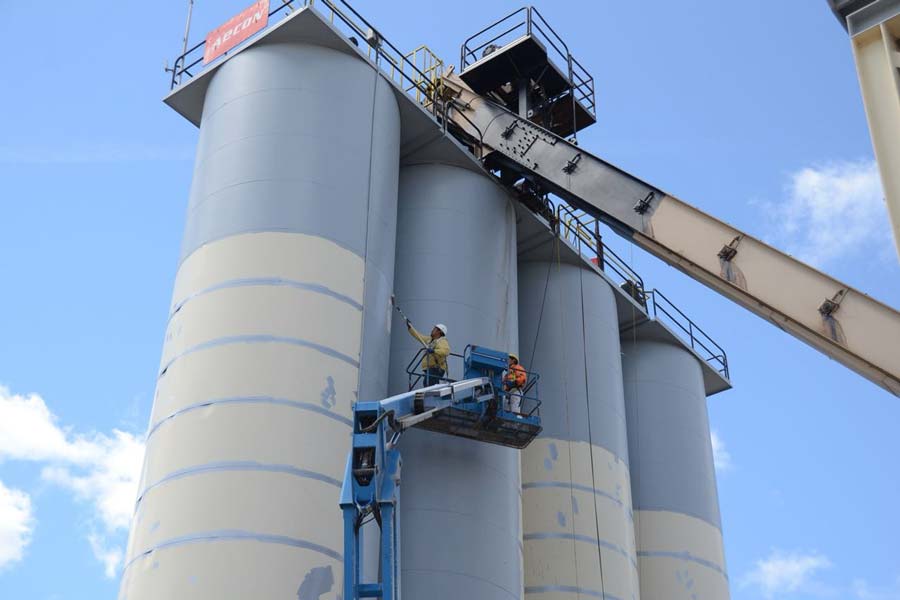
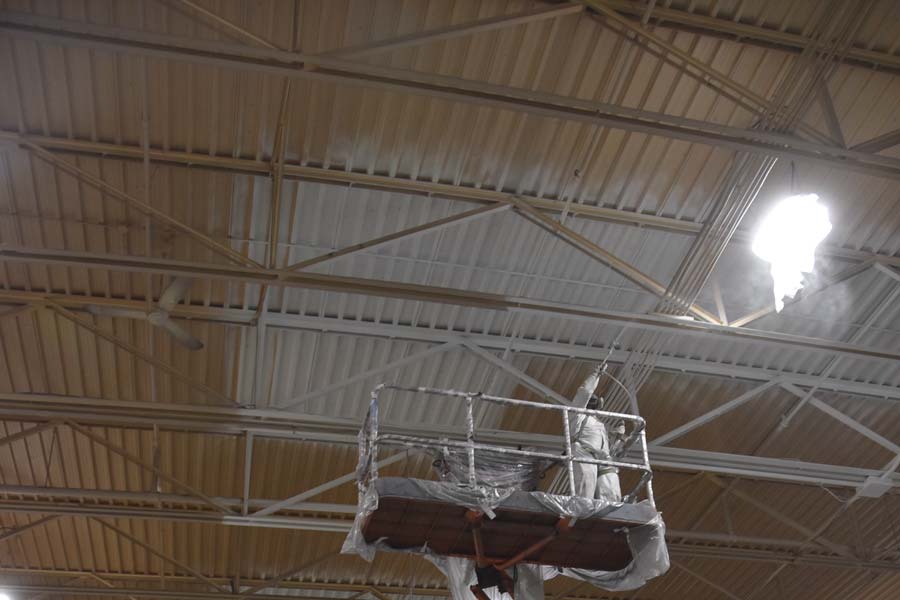
5. Touch-Up Painting: Touch-ups, such as covering minor scratches or blemishes, can maintain the appearance of the painted surface and prevent larger areas from requiring repainting.
6. Power Washing: For exterior surfaces, power washing can remove built-up grime and prevent the growth of mold or mildew, which can damage coated surfaces.
7. UV Protection: Using UV-resistant coatings can help prevent the fading and degradation of paint colours and finishes when exposed to sunlight.
8. Humidity and Temperature Control: Maintaining a controlled indoor environment can help prevent paint from peeling or cracking due to extreme humidity or temperature fluctuations.
9. Surface Preparation: Before repainting, proper surface preparation, such as sanding, priming, and cleaning, is essential to ensure good adhesion and a long-lasting coating job.
10. Regular Repainting: Over time, all paint will degrade, and surfaces will require repainting. Implementing a regular Maintenance Schedule can be an effective form of preventative maintenance to keep surfaces looking their best.
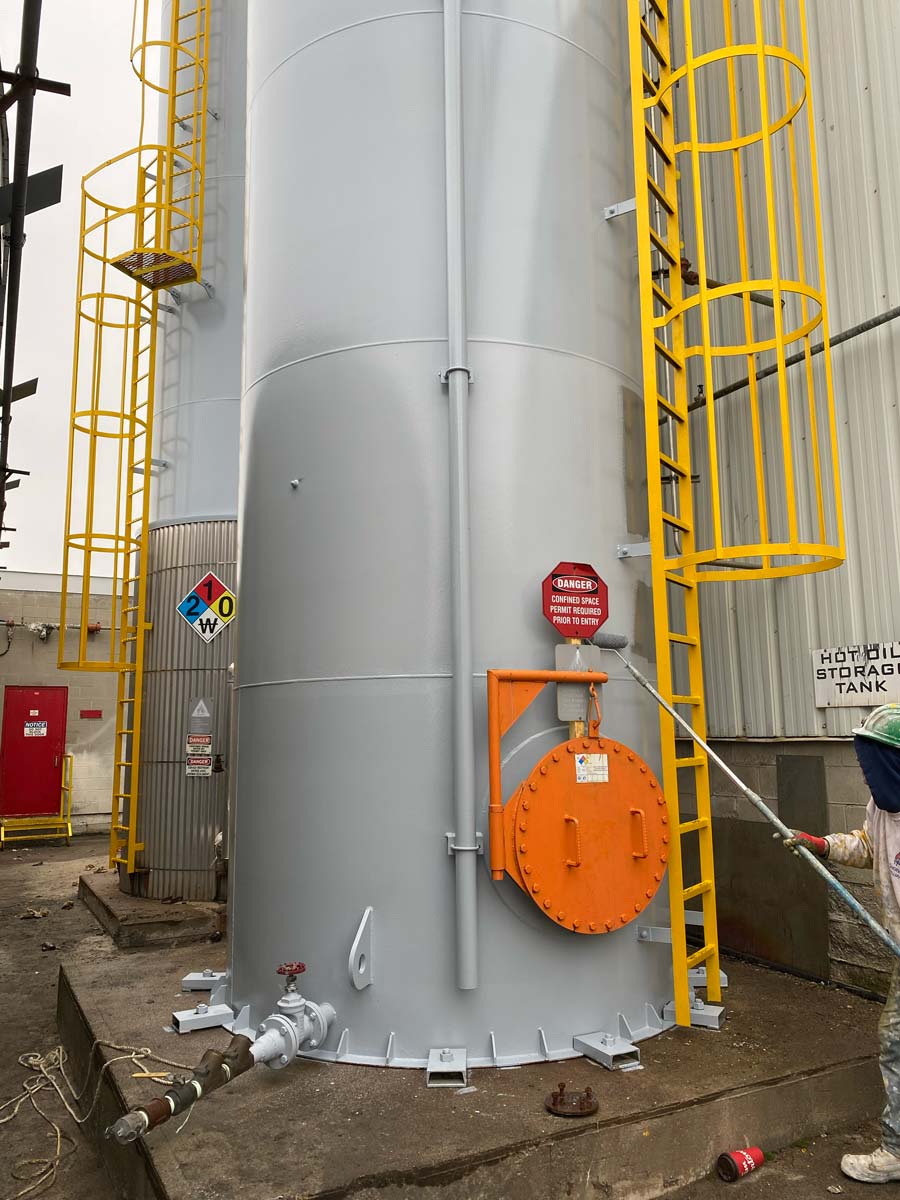
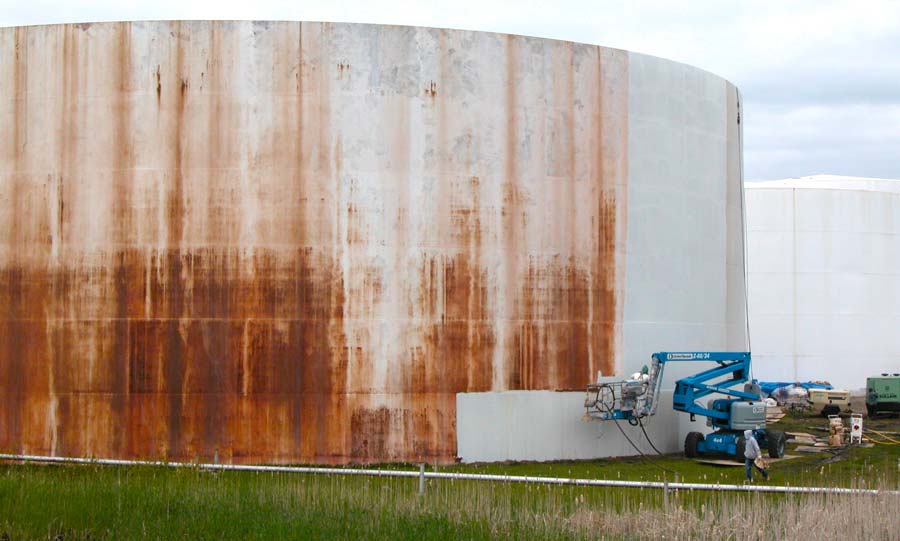
Importance
Preventative Maintenance is essential in industrial and commercial settings to protect and extend the life of coated surfaces, saving time and money in the long run by reducing the need for more extensive and costly repairs or complete repaints.
Contact us today to establish a cost-effective Maintenance Schedule with B.E.S.T. Painting Ltd.
ARTICLE:
Paint Maintenance Canada
Reduce Life-Cycle Expenses
Corrosion is a major, ubiquitous problem in many industry sectors, with a total cost estimated at $63 billion annually in Canada.
Contrary to popular belief, iron and steel structures aren’t the only ones affected by corrosion. The reaction of different materials with the environment results in corrosion affecting a wide range of metals and other materials, including rubber, plastics, composites, brick, and concrete.
Over time, corrosion may weaken industrial equipment pieces considerably, which become more prone to breakdowns and less safe for operators.
The best way to control corrosion and extend your industrial equipment’s life is to reapply a new coat of paint every few years. Moreover, having a paint maintenance program will allow you to protect your industrial equipment at a fraction of the cost it would take to repair or replace various machines.
This approach helps maintain the integrity and functionality of the equipment and contributes significantly to cost savings.