Toronto Silo Painters
Toronto Silo Painters
B.E.S.T.’s highly skilled team members provide Surface Preparation and Protective Coatings for Steel Silos, which are critical maintenance processes, whether they are used for storing liquids, gases, or dry materials. These processes are essential for several reasons:
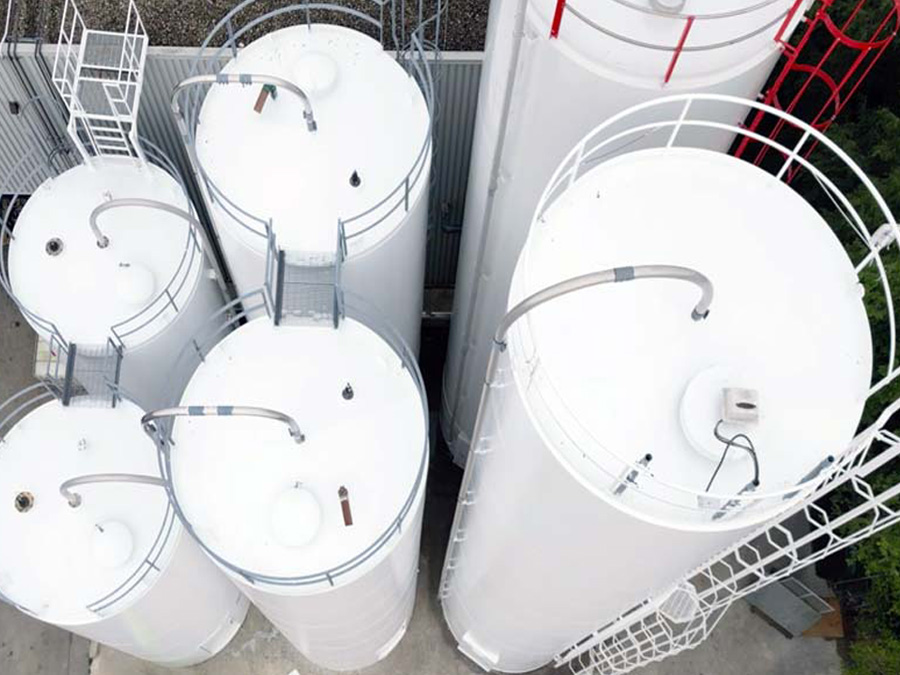
Why Choose Silo
Painting Services?
Corrosion Prevention: Silos are often exposed to harsh environmental conditions, such as moisture, chemicals, and temperature fluctuations.
Corrosion can severely compromise the structural integrity of these structures, leading to leaks and other safety hazards.
Protective coatings act as a barrier, preventing the substrate from coming into direct contact with corrosive elements, thereby reducing the risk of corrosion.
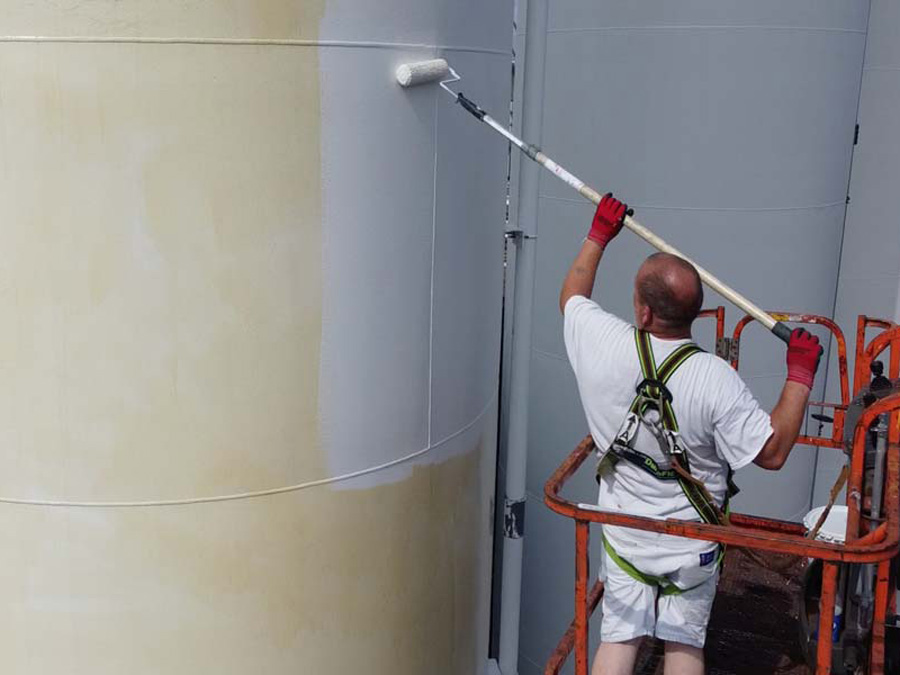
Longevity & Containment
Longevity:
Protective coatings extend a silo’s lifespan by reducing wear and slowing material degradation.
Containment:
Coatings form a barrier that prevents leaks and contamination, keeping stored materials safe and secure.
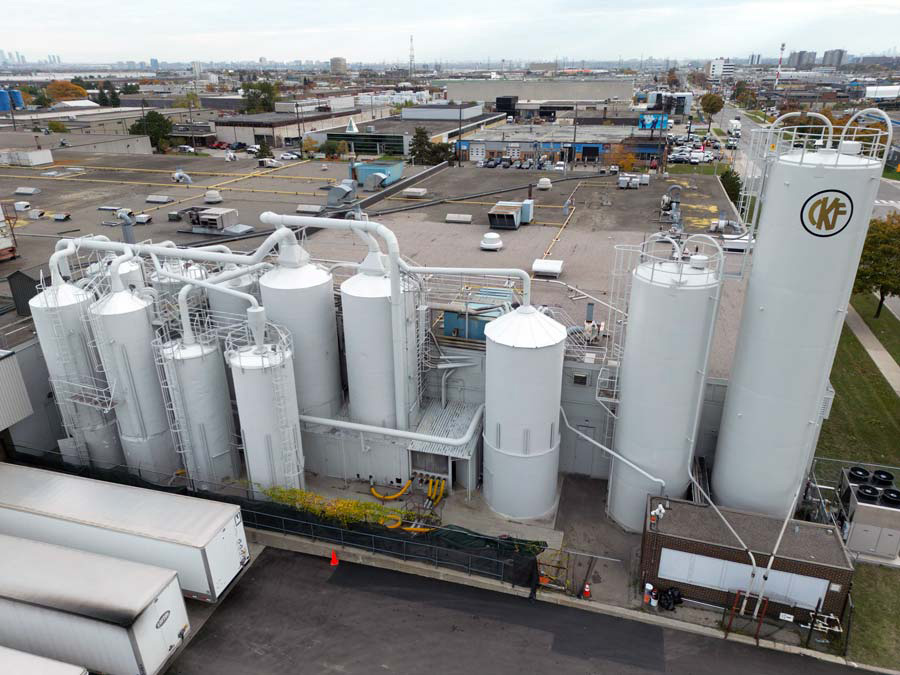
Aesthetic Upgrades & Branding
Aesthetic Appearance: In some cases, silos are visible to the public or located in aesthetically sensitive areas.
Protective coatings not only protect the structure but can also improve its appearance by providing a consistent and appealing finish.
Installation of corporate decals is an additional service B.E.S.T. excels at.
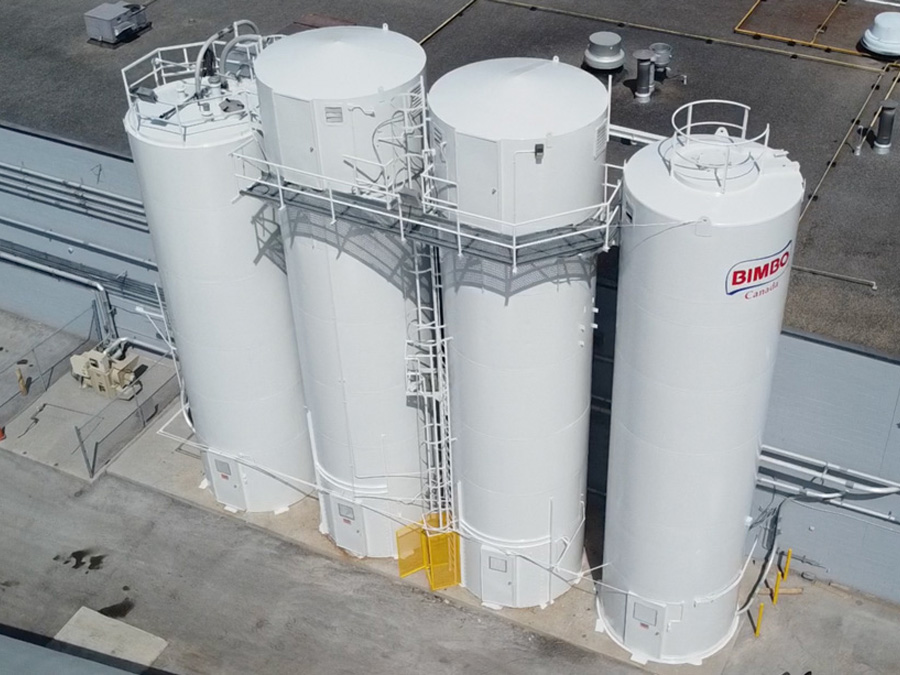
Surface Preparation:
Before applying protective coatings, it’s essential to remove dirt, rust, and old paint to create a clean, properly profiled surface.
Good prep ensures the coating adheres well and prevents future failures. Common methods include abrasive blasting, power washing, and chemical cleaning.
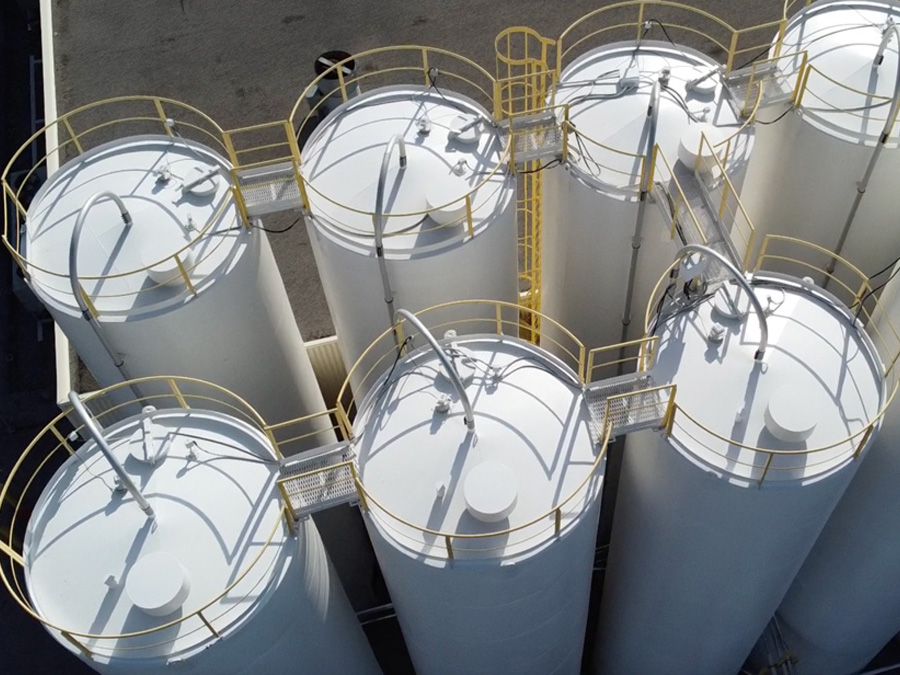
Surface Preparation
Before applying protective coatings, it’s essential to remove dirt, rust, and old paint to create a clean, properly profiled surface.
Good prep ensures the coating adheres well and prevents future failures. Common methods include abrasive blasting, power washing, and chemical cleaning.
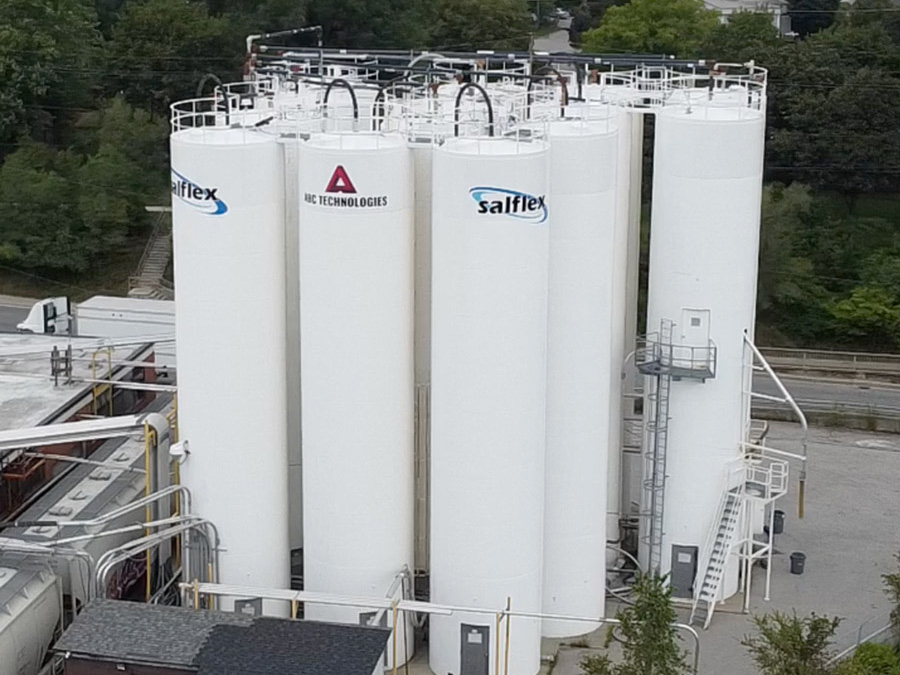
Aesthetic Appearance:
In some cases, silos are visible to the public or located in aesthetically sensitive areas.
Protective coatings not only protect the structure but can also improve its appearance by providing a consistent and appealing finish.
Installation of corporate decals is an additional service B.E.S.T. excels at.