Abrasive Blasting
Surface Preparation for Industrial and Commercial Applications
What is “Abrasive Blasting”?
Abrasive blasting, also known as sandblasting, is a crucial process in surface preparation. It involves propelling a high-velocity stream of abrasive particles at a surface to remove contaminants such as rust, scale, old paint, and dirt. This process creates a clean, profiled surface that promotes optimal adhesion for subsequent coatings.
Abrasive blasting is a versatile technique that can be applied to a wide range of surfaces, including metal, concrete, and wood. It is commonly used in various industries, such as construction, manufacturing, and shipbuilding.

Abrasive Blasting Toronto
At B.E.S.T. Painting Ltd., we specialize in delivering exceptional abrasive blasting and sandblasting services throughout Southern Ontario and the GTA. Our team of NACE Level 3 Coating Inspectors and experienced technicians guarantee top-quality results for every project.
With decades of industry experience, we understand the importance of proper surface preparation. Our rigorous QA/QC processes ensure that your assets are thoroughly cleaned and prepared to meet the highest standards.
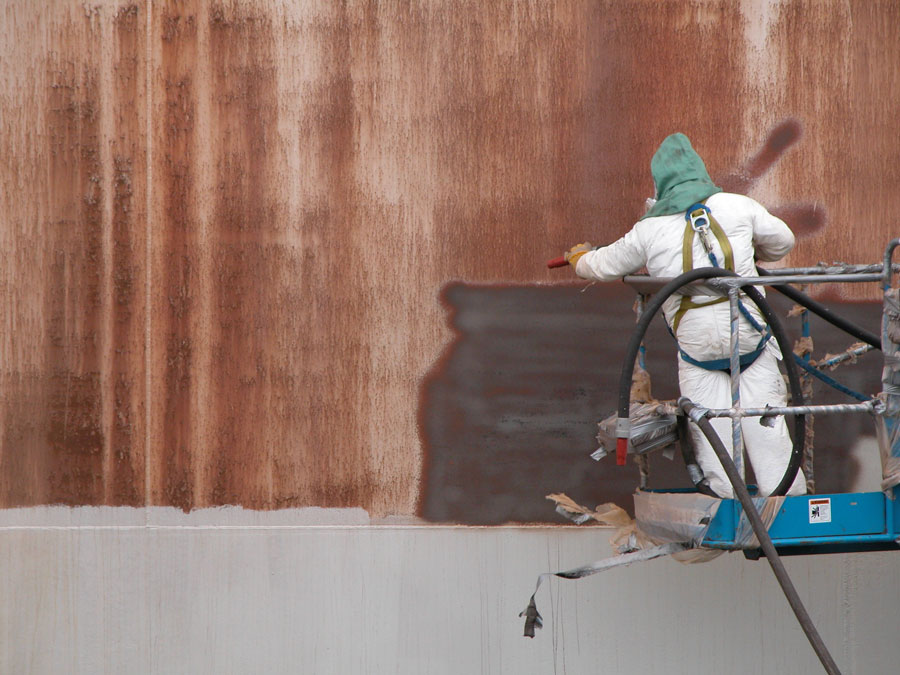
Benefits of Abrasive Blasting
Stronger Bonding: Prepped surfaces ensure coatings stick and last.
Durability: Removes grime and roughens surface for longer coating life.
Rust Protection: Blasts away corrosion to preserve your assets.
Cost-Effective: Saves on future recoating despite initial cost.
Eco-Safe: Cleaner than chemical stripping when done right.
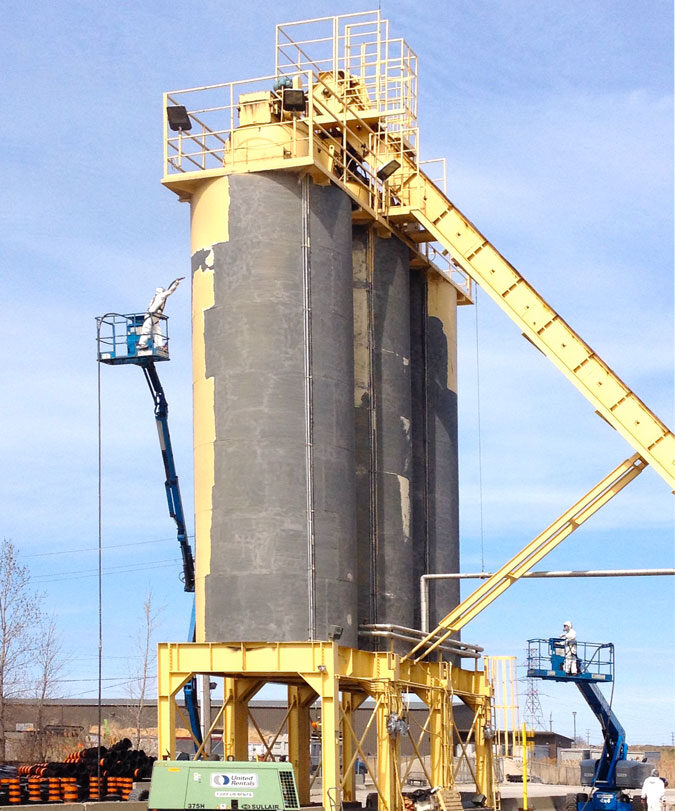
Why Choose B.E.S.T. Painting?
- NACE-Certified Experts: Our team is comprised of highly skilled professionals with extensive experience in abrasive blasting.
- State-of-the-Art Equipment: We utilize advanced equipment to deliver efficient and effective results.
- Commitment to Quality: We are dedicated to providing exceptional service and exceeding your expectations.
- Customer Satisfaction: Our focus on customer satisfaction has earned us a reputation as a leading provider of abrasive blasting services in Toronto.
When you choose B.E.S.T. Painting Ltd., you can expect:
- Expert knowledge and experience: Our team is well-versed in the latest techniques and industry standards.
- High-quality workmanship: We deliver precise and efficient abrasive blasting services.
- Attention to detail: We pay close attention to every aspect of the project.
- Competitive pricing: We offer affordable rates without compromising on quality.
What does
Abrasive Blasting do?
Abrasive blasting, or sandblasting, uses high-pressure abrasive materials to clean, smooth, or prepare surfaces by removing rust, paint, and grime.
Because abrasive blasting often creates an ideal surface for adhesion, it’s frequently followed by the application of a protective or functional coating. This coating can serve various purposes.